Metal Bending Design Rules
When you upload your flat pattern or 3D model, our system will automatically do a full manufacturability analysis and let you know if there are any problems or possible concerns.
Some problems can be design-specific (eg. lack of bend relief, causing potential "puckering" in your finished part where bends meet). And some problems may be specific to the capabilities and tooling OSH Cut currently has. In both cases, our system will communicate what the issues are.
Some common problems are described below:
Insufficient Flange Support
This error can occur if there are cutout regions where the die should be making contact with the part, but doesn't. The design below has tapered areas that prevent the die from properly making contact with the part, resulting in the flange support error:
In the part below, for example, there is contact with the die in the middle of the bend, but not on the edges.
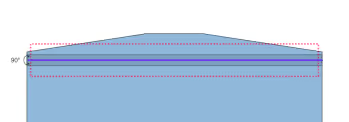
The red dotted line shows where the die needs to make contact with the part. Some amount of lost contact is allowed, but in this example, there is too much material not in contact with the die. Below, you can see how the tapered region is not in contact with the die:
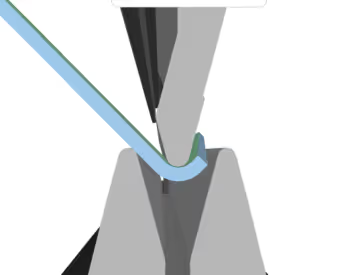
The same error can take place if there are too many internal cutouts on the interior of the part, where the die makes contact.
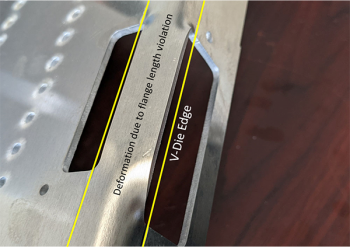
Internal cutouts can cause interior features to deform, and potentially cause the effective bend location to shift in one direction or another. For example, the part below has cutouts inside the die keepout region:

In the case above, it is likely that the bend will be pulled toward the hole on the left, because there is less material on that side to support the part. This will effectively elongate the part and cause the finished size to be out of spec (the dotted line surrounding the selected bend above indicates where the die will make contact with the part. The region shaded in yellow illustrates where the die will not fully support the part).
In a bending process, it is always best to ensure that parts do not have cutouts inside the die region.
Missing or Insufficient Bend Relief
Bend relief allows two bend regions to connect on the ends, without "fighting over" which bend gets to deform the metal. In the flat pattern below, two different bends at 90 degrees meet on the end of the part, without bend relief:
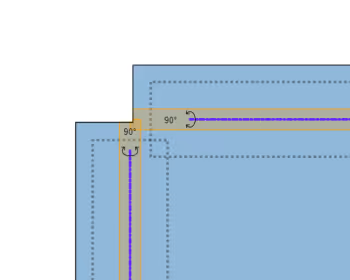
Shown above, the yellow regions show the area of the metal that will be bent on a radius (the gray dotted line shows where the die makes contact with the flat).
The yellow regions for both bends overlap on the edge of the part. This will cause both bends to attempt to deform the part, causing "puckering" in the overlapping region.
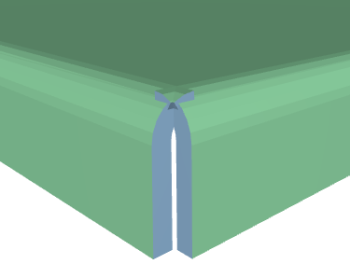
Shown above, both regions want to deform the part in the same area, causing the area to deform undesirably.
The fix for this problem is to add a cutout region where the bends meet, so that they can form independently:
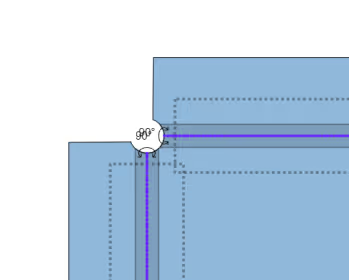
In the above, the circular cutout region keeps the bent regions isolated so that they don't interfere.
Collision With the Brake
Our system will report a collision with the brake if we don't have tooling that can perform your bends. You can click the animation icon in the top of the part view to show the bend simulation:
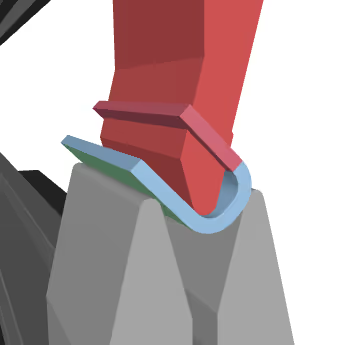
The order in which the bends are performed does have an impact on whether the part will collide with the brake. But our system checks every possibility, even if it's not showing you every possible bend sequence.
We have our eyes on more tooling to expand our bending capabilities, but what our system reports is accurate.
Part Self-Collision
Similar to a brake collision, this error takes place if our system detects that your part will collide with itself during bending. This can happen if two bent flanges are very close to each-other. Our system estimates the amount of overbend required to account for springback, and a part with tight flange positioning can cause collision during springback compensation.
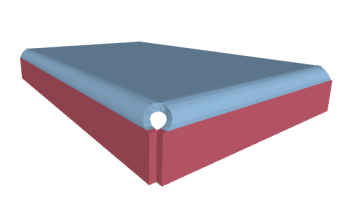
In the part above, the adjacent flanges (highlighted in red because they collide) collide during bending. Usually, you'll want to create a seam gap in your model, so that after bending, there is some clearance. That might look something like this:
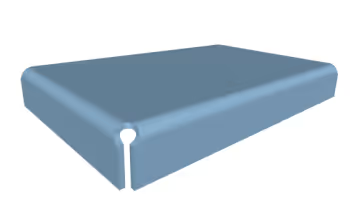
As shown above, there is plenty of space between adjacent flanges to ensure that they don't collide during bending.
Bends Too Close Together
If bends are placed too close together, we can't position the part above the die to perform one of the bends, after the first bend has been performed.
For example, this narrow, deep channel can't be formed in an air-bending process:
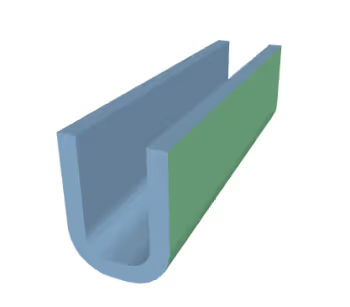
The first bend can be performed, but the second bend both collides with the punch, and violates minimum flange length rules to perform the second bend:
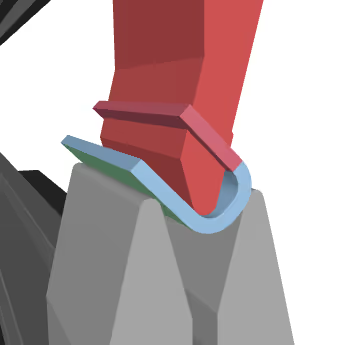
Lack of Gauging Surface
When positioning parts on the press brake for bending, we use two CNC (computer-controlled) back gauges as a reference. Placing the part flat against the back gauges ensures that the punch is aligned right where it needs to be.
Our system will analyze your bends and determine whether a good gauging surface exists. A gauging surface can be:
- A flat part edge parallel to the bend line, at least 0.25" long for small parts, or
- Two or more edge (flat or curved) that form a line that is parallel to the bend line
For example, the part below does not have a gauging surface and won't pass the manufacturability check:
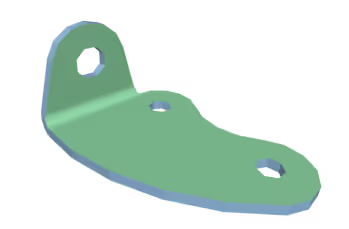
But the part below has a flat surface parallel to the bend, and can be manufactured:
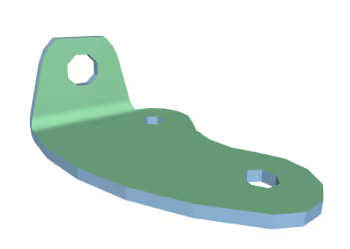
Gauging surfaces can be created by adding tabbed features to the part, to be removed after bending, or by cutting away or otherwise modifying the part profile so that there is a flat surface parallel to the bend line.
It is worth noting that parts without good gauging surfaces can be manufactured, but at the expense of custom-designed jigs to hold parts in place during bending. That would be an acceptable option for a production run, but a very expensive option for parts manufactured on-demand on short lead-times. Consequently, it is not a service that OSH Cut offers at this time.